The widespread adoption of electric forklift in various industrial sectors underscores their efficiency, eco-friendliness, and cost-effectiveness. Yet, to uphold their optimal performance and extend their lifespan, diligent maintenance is paramount. In this comprehensive guide, we’ll delve into essential tips and best practices for maintaining an electric forklift in Singapore. By implementing these strategies, you can ensure sustained productivity, minimise downtime, and enhance workplace safety.
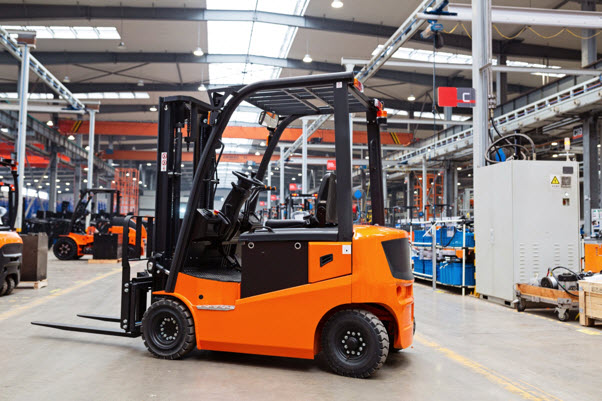
Regular Inspection
Routine inspections serve as the frontline defence against potential issues, helping to identify problems early and prevent costly repairs. Let’s break down the components and inspection points for a thorough electric forklift assessment:
Component | Inspection Points |
Battery | Check for corrosion, leaks, and maintain electrolyte levels |
Cables | Inspect for fraying, damage, and ensure secure connections |
Hydraulic System | Examine for leaks and maintain appropriate fluid levels |
Brakes | Test functionality and adjust as necessary |
Tires | Assess wear and tear, ensure proper inflation |
Electrical System | Inspect for loose connections and damaged wires |
Controls | Verify proper functioning of all controls |
Battery Maintenance
The battery serves as the powerhouse of an electric forklift, demanding meticulous care to optimise performance and lifespan. Here’s a closer look at the key aspects of battery maintenance:
- Electrolyte Levels: Regularly monitor electrolyte levels in each individual cell of the battery, ensuring they are within the recommended range. Replenish with distilled water as necessary, taking care not to overfill or underfill, to maintain proper chemical balance and electrolyte conductivity.
- Terminal Cleaning: Utilise appropriate cleaning agents and tools to remove corrosion and build-up from battery terminals effectively. Apply terminal protection products to inhibit future corrosion, promoting reliable electrical connections and reducing the risk of voltage drops or intermittent power supply.
- Equalisation: Implement a controlled equalisation process at regular intervals, typically using specialised charging equipment, to balance the charge among battery cells. This procedure helps prevent capacity imbalances, minimises sulfation, and maximises the usable capacity and lifespan of the battery.
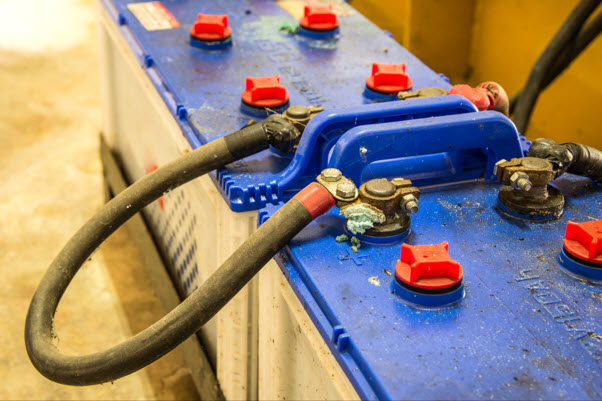
- Discharge Management: Establish discharge thresholds and monitoring systems to prevent the battery from reaching critically low voltage levels. Implement smart charging algorithms or battery management systems to optimise charge and discharge cycles, reducing stress on the battery and prolonging its operational life.
- Storage: Store batteries in dedicated battery rooms or racks equipped with temperature and humidity controls to minimise degradation. Implement rotation schedules to ensure older batteries are not left in storage for extended periods, reducing the risk of sulfation and self-discharge. Additionally, consider implementing battery maintenance systems that periodically charge and discharge stored batteries to maintain optimal condition.
Charging Practices
Proper charging practices are critical for preserving battery health and ensuring uninterrupted operation. Consider the following guidelines:
- Manufacturer’s Specifications: Adhere strictly to the manufacturer’s charging guidelines, including recommended charge rates, voltage limits, and charging algorithms. Consider utilising smart chargers or charging systems specifically designed for the battery type and application to maximise charging efficiency and battery lifespan.
- Avoid Overcharging / Undercharging: Implement charge monitoring systems or timers to prevent overcharging or undercharging, which can lead to electrolyte stratification, plate sulfation, and reduced battery capacity. Utilise voltage and temperature sensing devices to terminate charging cycles accurately and prevent overvoltage conditions.
- Charging Stations: Install dedicated charging stations equipped with safety features such as overcurrent protection, ground fault detection, and ventilation systems to dissipate heat generated during charging. Ensure proper spacing between charging stations to prevent overheating and minimise the risk of thermal runaway events.
- Cooling Period: Allow batteries to cool to ambient temperature before initiating charging cycles, especially after heavy usage or fast charging sessions. Implement temperature monitoring systems to ensure batteries are within the recommended temperature range before charging, preventing thermal stress and prolonging battery life.
- Battery Rotation: Develop a battery rotation schedule based on usage patterns and battery health metrics to distribute usage evenly among multiple batteries. Implement RFID or barcode tracking systems to monitor battery usage and charging cycles accurately, optimising battery lifespan and reducing overall operating costs.
Operator Training
Competently trained operators are essential for maintaining electric forklifts and ensuring workplace safety. Prioritise comprehensive training covering:
- Operation Proficiency: Provide comprehensive training programs covering safe forklift operation techniques, including proper acceleration, braking, steering, and load handling procedures. Incorporate practical hands-on training sessions to reinforce theoretical knowledge and promote skill development.
- Maintenance Awareness: Educate operators on how to perform visual inspections and basic maintenance tasks such as checking fluid levels, inspecting tires, and identifying signs of wear or damage. Encourage a proactive approach to maintenance by emphasising the importance of early detection and timely intervention to prevent equipment downtime and costly repairs.
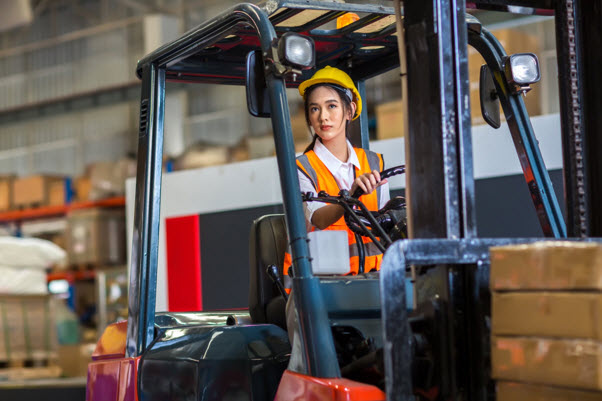
- Charging Safety: Conduct training sessions focusing on safe charging practices, including proper battery handling, connection procedures, and emergency response protocols. Emphasise the importance of wearing appropriate personal protective equipment (PPE) and following manufacturer guidelines to minimise the risk of electrical hazards and acid exposure during charging operations.
- Emergency Response: Train operators to recognize and respond effectively to emergency situations, including fire outbreaks, chemical spills, and equipment malfunctions. Provide instruction on emergency shutdown procedures, evacuation protocols, and first aid techniques to ensure the safety of personnel and minimise property damage in the event of an accident.
Documentation and Record Keeping
Comprehensive documentation of maintenance activities and inspections is crucial for monitoring forklift performance and regulatory compliance. Establish a structured maintenance log that includes:
- Dates and Details: Maintain a centralised database or logbook containing detailed records of all maintenance activities and inspections, including dates, times, locations, and personnel involved. Implement digital record-keeping systems to facilitate data retrieval, analysis, and reporting, ensuring compliance with regulatory requirements and industry standards.
- Repairs and Replacements: Document all repair and replacement activities performed on forklifts and associated equipment, including parts used, labour hours, and costs incurred. Implement asset tracking systems to monitor equipment downtime, repair histories, and warranty information, enabling informed decision-making and cost analysis.
- Battery Maintenance Records: Keep comprehensive records of all battery-related maintenance activities, including charging cycles, equalisation procedures, voltage readings, and electrolyte level adjustments. Use electronic data loggers or cloud-based monitoring platforms to track battery performance metrics in real-time, identifying potential issues and optimising maintenance schedules.
- Operator Training Records: Maintain up-to-date records of operator training sessions attended, certifications obtained, and competency assessments completed. Utilise learning management systems (LMS) or training record databases to track individual training progress, schedule refresher courses, and ensure compliance with regulatory training requirements.
Conclusion
Efficient and safe operation of electric forklift hinges on diligent maintenance practices. By adhering to the tips and best practices outlined in this guide, you can optimise Forklift Singapore‘s performance, extend its lifespan, and enhance workplace safety. Prioritise regular inspections, emphasise battery maintenance, adhere to correct charging procedures, invest in operator training, and maintain meticulous documentation. For expert assistance and reliable equipment, consider UMW Equipment. You can contact at +(65) 6265 3155 or via email at sales@umweepl.com.sg. By proactively addressing maintenance needs with trusted partners like UMW Equipment, you can minimise downtime, reduce repair costs, and maximise operational efficiency, ultimately bolstering productivity and profitability.